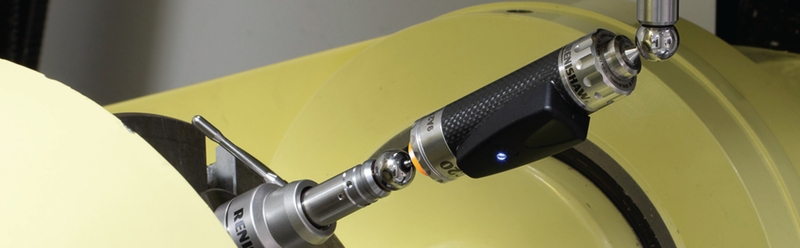
Renishaw Barball Calibration
For those committed to maintaining the precision of their CNC machine, the Renishaw QC20 ballbar is a highly recommended tool for calibrating according to ISO 10791-6 standards. Calibration upkeep plays a pivotal role in ensuring the optimal performance of your CNC machine.
Our suggestion is to conduct three ballbar tests to assess the machine’s proficiency in the X, Y, and Z axes, examining two planes with each evaluation. This comprehensive approach provides a thorough analysis, uncovering up to 23 distinct machine errors. Display the test results on the machine using the provided Renishaw stickers. While it offers a straightforward visual representation, it serves as undeniable evidence that the machine has undergone testing and is capable of producing accurate parts. This means customers can focus solely on tooling, fixturing, and programming, without concerns about the machine’s performance.
The Ballbar 20 software, bundled with the QC20-W ballbar system, boasts backward compatibility. This allows comparison of previously collected data with the older Ballbar 5 software to the new QC20-W data. This feature is particularly valuable for companies with extensive historical data from QC10 ballbar tests, enabling a like-for-like comparison with the latest data.
The software performs a detailed analysis, pinpointing machine errors such as ball screw preload. It provides options for repair or calibration, offering insights that can help anticipate and prevent costly major repairs through corrective maintenance.
![]() |
![]() |
![]() |
Laser Calibration at the Speed of Light
The term “laser” suggests speed, but the reality of a bi-directional laser calibration on a CNC mill’s linear axis is far from light speed. A 1 m axis can take 30 to 60 minutes, with pauses of up to 23 seconds between 10 mm increments, causing significant downtime for large, high-value assets, a major concern for machine shop owners. Depending on machine crashes and the quality system, annual laser calibrations can keep machines out of action for days.
Renishaw’s solution, utilizing the XL-80 laser interferometer, reduces settling time to just 250 milliseconds after each axis move, slashing calibration times by 85-95 percent. This not only minimizes downtime on production assets but also enhances accuracy in actual cutting conditions, where tool engagement
occurs without settling time.
To implement this high-speed calibration, a machine’s CNC can use an M-code to trigger the laser, a standard feature on many CNCs. Renishaw’s Calibration Business Manager, Michael Wilm, notes, “The laser simply needs to see the relay close for as little as a microsecond; any chatter within 20 milliseconds gets ignored, the laser takes a reading, and the axis moves to the next measuring position.”
This high-speed data capture technique isn’t limited to CNCs and can be customized for other equipment, offering an efficient solution to reduce overall machine downtime.
![]() |
![]() |